- March 31, 2024
- Posted by: Waldon Fenster
- Categories: Labor, Manufacturing
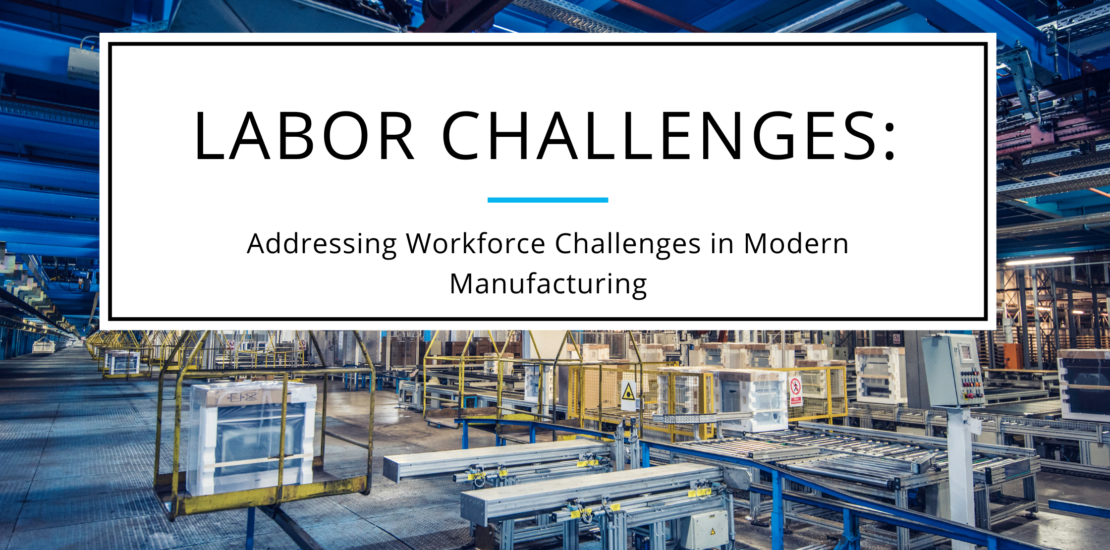
Labor Challenges: Addressing Workforce Challenges in Modern Manufacturing
In the dynamic landscape of modern manufacturing, addressing labor challenges is paramount for sustained success. As technology evolves and demographics shift, manufacturers face an array of workforce-related hurdles. Understanding and proactively managing these challenges are crucial for maintaining competitiveness and driving growth.
Understanding Labor Challenges in Modern Manufacturing
Definition of labor challenges
Labor challenges encompass a spectrum of issues related to workforce management and optimization. From recruitment and retention to skills development and operational efficiency, these challenges are multifaceted and require strategic solutions.
Overview of the current landscape of the manufacturing industry
The manufacturing industry is undergoing rapid transformation, fueled by advancements in technology, globalization, and changing consumer demands. Amidst this evolution, manufacturers are grappling with an array of labor-related obstacles that impact productivity, efficiency, and profitability.
Identification of common labor challenges faced by manufacturers
Manufacturers commonly encounter challenges such as skill shortages, workforce turnover, and adapting to technological advancements. These challenges can hinder operational effectiveness and impede growth if not addressed proactively.
Factors Contributing to Labor Challenges
Technological advancements and automation
Advancements in automation and digitalization have revolutionized manufacturing processes, requiring workers to possess increasingly specialized skills. While automation enhances productivity, it also necessitates ongoing training and upskilling to ensure workforce readiness.
Skill gaps and workforce shortages
Skill gaps and workforce shortages are prevalent in the manufacturing sector, exacerbated by factors such as an aging workforce and inadequate education and training programs. Addressing these gaps requires collaborative efforts between industry stakeholders, educational institutions, and policymakers.
Changing demographics and workforce preferences
Demographic shifts, including an aging workforce and changing preferences among younger workers, pose challenges for manufacturers in attracting and retaining talent. To remain competitive, manufacturers must adapt their recruitment and retention strategies to align with evolving workforce dynamics.
Impact of Labor Challenges on Manufacturing Operations
Decreased productivity and efficiency
Labor challenges can lead to decreased productivity and efficiency, resulting in production delays, increased costs, and lost revenue opportunities. Addressing these challenges requires a holistic approach that encompasses both operational and human capital considerations.
Increased costs and operational disruptions
Labor-related issues such as turnover and skill shortages can drive up recruitment and training costs, impacting profitability. Additionally, operational disruptions stemming from workforce shortages or skill mismatches can hinder production schedules and customer satisfaction.
Difficulty in attracting and retaining talent
In a competitive labor market, attracting and retaining skilled workers poses a significant challenge for manufacturers. Failure to offer competitive wages, benefits, and career advancement opportunities can result in high turnover rates and talent shortages.
Strategies for Addressing Labor Challenges
Investment in workforce training and development
Proactive investment in workforce training and development is essential for addressing skill gaps and enhancing workforce capabilities. Implementing robust upskilling and reskilling programs ensures that employees are equipped with the necessary skills to thrive in an evolving manufacturing landscape.
Embracing automation and technology
Embracing automation and technology enables manufacturers to improve productivity, quality, and efficiency. By integrating robotics, artificial intelligence, and other advanced technologies into their operations, manufacturers can streamline processes and mitigate labor-related challenges.
Enhancing recruitment and retention efforts
Effective recruitment and retention strategies are critical for attracting and retaining top talent. Offering competitive wages, benefits, and career advancement opportunities, as well as fostering a positive work culture, can help manufacturers attract and retain skilled workers.
Leveraging workforce analytics and data-driven insights
Leveraging workforce analytics and data-driven insights enables manufacturers to make informed decisions about their human capital strategies. By analyzing workforce trends, identifying skill gaps, and forecasting future labor needs, manufacturers can optimize their workforce planning and management.
Case Studies: Successful Approaches to Addressing Labor Challenges
Example 1: Toyota’s Training and Development Programs
Toyota has long been regarded as a pioneer in workforce development within the manufacturing industry. Through its comprehensive training and development programs, Toyota has successfully addressed labor challenges by equipping employees with advanced technical skills and fostering a culture of continuous improvement.
By providing training in areas such as lean manufacturing principles, problem-solving methodologies, and advanced automation technologies, Toyota has empowered its workforce to adapt to evolving manufacturing processes and technologies. This focus on upskilling has not only enhanced employee capabilities but has also contributed to improved operational efficiency and quality control across Toyota’s manufacturing facilities.
Example 2: Siemens’ Implementation of Digital Twins
Siemens, a global leader in industrial automation, has revolutionized its manufacturing operations through the adoption of digital twin technology. By creating virtual replicas of physical assets and processes, Siemens has gained unprecedented insight into its manufacturing operations, enabling proactive decision-making and optimization.
Through the use of digital twins, Siemens has been able to identify and address potential issues before they escalate, minimize downtime, and optimize production schedules. This innovative approach to automation has not only improved productivity but has also reduced reliance on manual labor, thereby mitigating labor challenges associated with workforce shortages and skill gaps.
Example 3: Tesla’s Approach to Recruitment and Retention
Tesla, known for its groundbreaking electric vehicles, has implemented innovative recruitment and retention strategies to attract and retain top talent in a competitive market. By offering competitive compensation packages, opportunities for career advancement, and a dynamic work environment, Tesla has been able to attract skilled professionals from diverse backgrounds.
Additionally, Tesla’s commitment to employee well-being and development, including offering flexible work arrangements and professional development opportunities, has contributed to high levels of employee satisfaction and engagement. By prioritizing recruitment and retention efforts, Tesla has successfully mitigated labor challenges and positioned itself as a leader in the automotive industry.
Future Outlook: Navigating Labor Challenges in an Evolving Manufacturing Landscape
Anticipated trends and developments in labor challenges
As manufacturing continues to evolve, labor challenges will persist and evolve alongside technological advancements, demographic shifts, and changing consumer preferences. Manufacturers must remain agile and proactive in addressing these challenges to thrive in a competitive marketplace.
Strategies for staying agile and adaptable in addressing future labor challenges
To navigate future labor challenges, manufacturers must prioritize continuous innovation, investment in workforce development, and strategic partnerships with educational institutions and industry peers. By embracing change and leveraging emerging technologies, manufacturers can position themselves for long-term success.
Conclusion
In conclusion, addressing labor challenges is imperative for modern manufacturers seeking to maintain competitiveness and drive growth. By understanding the factors contributing to labor challenges, implementing strategic solutions, and staying ahead of emerging trends, manufacturers can overcome obstacles and thrive in an ever-evolving landscape. With proactive management and a commitment to workforce excellence, manufacturers can position themselves for sustained success in the dynamic world of modern manufacturing.
-
Read Full Article; https://dealexchange.com/addressing-workforce-challenges-in-modern-manufacturing
-
Have a business for sell off market? Complete this intake form; Opportunity – Deal Exchange
#ManufacturingChallenges, #WorkforceDevelopment, #AutomationTechnology, #SkillGapSolutions, #FutureOfWork, #LaborManagement, #IndustryInnovation