- April 10, 2024
- Posted by: Waldon Fenster
- Categories: Equipment, Manufacturing
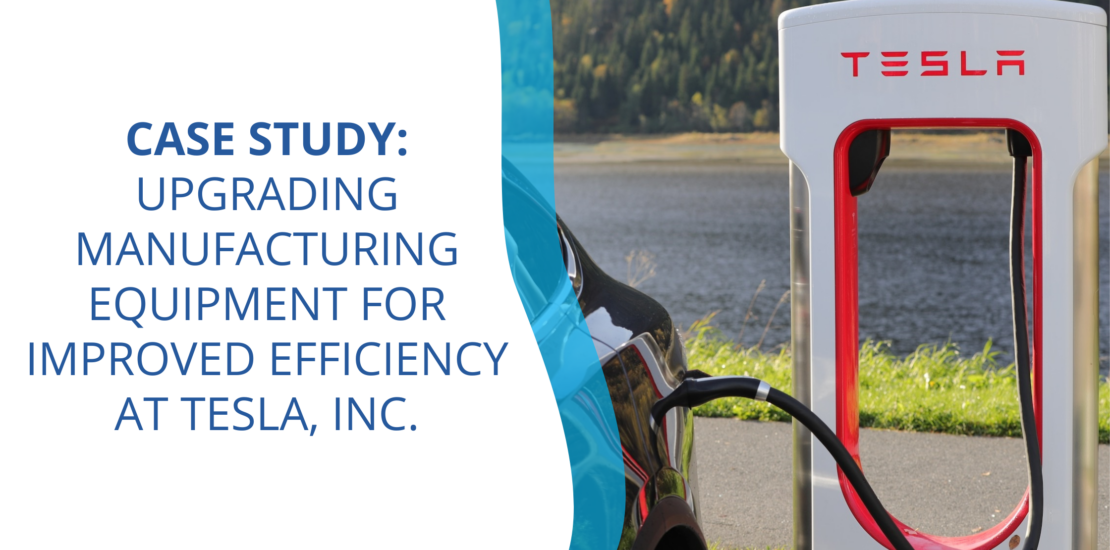
Case Study: Upgrading Manufacturing Equipment for Improved Efficiency at Tesla, Inc.
Introduction
In today’s competitive manufacturing landscape, efficiency is paramount. Tesla, Inc., a pioneer in electric vehicles and renewable energy, exemplifies the transformative power of upgrading manufacturing equipment. This case study delves into Tesla’s journey towards enhanced efficiency through strategic equipment upgrades. By investing in cutting-edge technology and innovative processes, Tesla has revolutionized its manufacturing operations, setting a benchmark for the industry.
Understanding the Need for Upgrading Manufacturing Equipment
Outdated manufacturing equipment can stifle progress and hinder productivity. For Tesla, Inc., the challenges posed by obsolete machinery were significant obstacles to achieving its ambitious production targets. Recognizing the critical role of modern equipment in driving efficiency, Tesla embarked on a comprehensive evaluation of its manufacturing infrastructure. The company identified bottlenecks, quality control issues, and inefficiencies that could be addressed through equipment upgrades. Tesla understood that leveraging technological advancements presented an opportunity to enhance productivity, reduce costs, and maintain its competitive edge in the rapidly evolving automotive industry.
Case Study: Tesla’s Journey Towards Efficiency
Tesla’s pursuit of efficiency was driven by a commitment to innovation and excellence. Faced with the imperative to meet growing demand for its electric vehicles, Tesla initiated a strategic initiative to upgrade its manufacturing equipment. This marked the beginning of a transformative journey towards heightened efficiency and productivity. Tesla’s leadership recognized that upgrading equipment was not merely an operational necessity but a strategic imperative to sustain its market leadership position. The company embarked on a thorough assessment of its existing equipment, identifying areas for improvement and opportunities for optimization. Through meticulous planning and execution, Tesla laid the groundwork for a comprehensive upgrade initiative that would revolutionize its manufacturing processes.
Assessing the Options: Evaluating Upgrading vs. Replacement
When considering options for upgrading its manufacturing equipment, Tesla meticulously evaluated the merits of upgrading versus replacing existing machinery. The company recognized that both options had their advantages and drawbacks, and a thorough cost-benefit analysis was essential to inform its decision-making process. While replacing outdated equipment with state-of-the-art alternatives seemed enticing, Tesla also acknowledged the significant financial investment and potential disruption to operations associated with such a transition. Conversely, upgrading existing equipment offered the opportunity to leverage technological advancements while minimizing costs and operational disruptions. Ultimately, Tesla’s commitment to sustainability and operational efficiency guided its decision to prioritize equipment upgrades over replacement, aligning with its long-term strategic objectives.
Implementing the Upgrade: Tesla’s Experience
Implementing the equipment upgrade initiative required meticulous planning, coordination, and collaboration across various departments within Tesla. The company formed multidisciplinary teams comprising engineers, technicians, and procurement specialists to oversee the execution of the project. Tesla also established strategic partnerships with technology vendors and equipment suppliers to ensure access to cutting-edge solutions tailored to its specific needs. Throughout the implementation process, Tesla prioritized seamless integration and minimal disruption to ongoing operations.
Despite encountering challenges such as logistical constraints and technical complexities, Tesla’s agile approach and proactive problem-solving capabilities enabled it to overcome obstacles effectively. The company leveraged best practices in project management and change management to facilitate a smooth transition to upgraded equipment. By fostering a culture of innovation and continuous improvement, Tesla instilled a sense of ownership and accountability among its workforce, driving engagement and productivity. The successful implementation of the equipment upgrade initiative underscored Tesla’s commitment to operational excellence and reinforced its reputation as a leader in technological innovation.
Results and Impact of the Upgrade
The impact of Tesla’s equipment upgrades was multifaceted, yielding tangible improvements across various aspects of its manufacturing operations. Enhanced production efficiency, increased throughput, and improved product quality were among the primary benefits realized. Tesla’s upgraded equipment enabled it to streamline manufacturing processes, reduce cycle times, and optimize resource utilization. The company also experienced a significant reduction in operating costs attributable to improved energy efficiency and lower maintenance requirements. Moreover, the enhanced reliability and performance of the upgraded equipment contributed to a more robust supply chain and improved customer satisfaction. By leveraging cutting-edge technology and innovative solutions, Tesla strengthened its competitive position in the electric vehicle market and reaffirmed its commitment to driving sustainable growth and innovation.
Lessons Learned and Best Practices
Strategic Planning:
Tesla’s success underscores the importance of strategic planning in equipment upgrades. By meticulously analyzing their needs and aligning upgrades with long-term goals, Tesla maximized the impact of their investments.
Stakeholder Engagement:
Tesla actively engaged stakeholders throughout the upgrade process, fostering buy-in and ensuring alignment with organizational objectives. This collaborative approach facilitated smoother implementation and enhanced overall effectiveness.
Investment in Workforce Development:
Tesla recognized the critical role of its workforce in driving operational excellence. Through training and development initiatives, Tesla equipped its employees with the skills and knowledge needed to leverage new technologies and optimize processes.
Continuous Improvement and Agility:
Tesla’s proactive approach to addressing operational challenges highlights the value of continuous improvement and agility. By embracing change and adapting swiftly to evolving market dynamics, Tesla remained at the forefront of innovation and maintained a competitive edge.
Emphasis on Collaboration and Knowledge Sharing:
Tesla’s emphasis on collaboration and knowledge sharing fosters a culture of innovation and drives organizational resilience. By fostering an environment where ideas are freely exchanged and lessons learned are shared, Tesla harnesses the collective intelligence of its workforce to drive continuous improvement and innovation.
Embracing Technological Advancements:
Tesla’s success underscores the importance of embracing technological advancements in driving efficiency and competitiveness. By leveraging cutting-edge technologies and innovative solutions, companies can unlock new opportunities for growth and differentiation in the global marketplace.
Prioritizing Sustainability:
Tesla’s commitment to sustainability sets a powerful example for manufacturers worldwide. By prioritizing sustainability in equipment upgrades and operations, companies can not only reduce their environmental footprint but also enhance operational efficiency and long-term viability.
Conclusion
In conclusion, Tesla’s journey towards improved efficiency through equipment upgrades exemplifies the transformative impact of innovation and strategic investment. By prioritizing modernization and leveraging cutting-edge technology, Tesla has redefined the standards for operational excellence in the automotive industry. The company’s commitment to sustainability, innovation, and customer-centricity positions it for continued success and leadership in the years to come. As manufacturers navigate the complexities of an increasingly competitive landscape, Tesla’s example serves as a guiding light, inspiring organizations to embrace change, drive innovation, and unlock new opportunities for growth and success.
-
Read Full Article; https://dealexchange.com/case-study-upgrading-manufacturing-equipment-for-improved-efficiency-at-tesla-inc
-
Have a business for sell off market? Complete this intake form; Opportunity – Deal Exchange
#Tesla #ManufacturingEfficiency #EquipmentUpgrade #Innovation #Sustainability #ElectricVehicles #OperationalExcellence